UniCan: Breakthrough in aerosol packaging
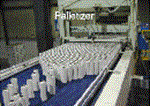
By Bill Noone,
Managing Editor, PackagingNetwork.com
The founders of Dispensing Containers set out to apply D&I two-piece technology to steel aerosol cans. The result is the UniCan — the next stage in the evolution of aerosol cans.
Contents
D&I technology for aerosols
Functional patent
Reduction of metal
Bend and crush
One line up, two to go
Next stage of evolution
Dispensing Containers Corp., which opened a new 114,000-sqft facility in Allentown, PA, earlier this year for the production of its innovative UniCan, believes it's onto something big — or shall we say, thin — in the aerosol packaging industry.
"There's no reason why this product can't do to the aerosol business what the D&I (drawn-and-ironed) beverage can did to beer and soda cans," says Edward J. Fitzgerald, president and CEO of DCC. "At the end of the day, we have a better can that can be made at a lower cost."
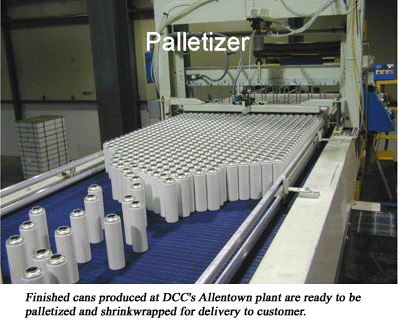
DCC's patented new UniCan is truly unique. A two-piece, thin-walled steel D&I can combined with a traditional aerosol dispensing mechanism, it is the only D&I aerosol can manufactured in the United States, says DCC's Leonard D. Ross, business development manager. Produced much like a beverage can and sleeker and lighter weight than conventional three-piece welded aerosol cans, UniCan is covered by a patent received by company founders George Diamond and Ralph Helmrich.
D&I technology for aerosols
In the United States, the aerosol can industry consists of 3.2 billion units — about 85% of which are three-piece welded steel cans, according to Ross. The remaining 15% are aluminum impact-extruded containers. Ross says that about a decade ago Diamond and Helmrich set out to apply D&I two-piece technology — typically used in the beverage can industry with aluminum — to steel aerosol cans.
"Even though most beverage cans in the U.S. are aluminum, to make an aerosol can with thin-walled aluminum would not satisfy the pressure requirements because aluminum is a relatively soft metal," notes Ross. However, most beverage cans made in Europe use steel, as do food cans in the U.S., which are made on D&I lines, so the D&I process is equally amenable to this material.
Working with steel to achieve the material savings of thinning the container wall, Diamond and Helmrich developed the UniCan technology over a number of years and incorporated Dispensing Containers Corp. in the early 1990s. In 1993 the company was granted the primary patent for the DCC technology. After raising seed capital, the two founders built a pilot manufacturing line for the UniCan in Glen Gardner, NJ. Eventually, after further development, the company ordered its first line and launched its first plant, the Allentown plant, which opened in May.
Functional patent
DCC's patent, says Ross, is a functional one. "It has nothing to do with the canmaking process or what the can is made of," he says. "The primary claim of the patent has to do with the functionality of the finished product. When the can is full with ingredient it is rigid to the hand as a result of the internal pressure of the container, and it maintains its rigidity throughout the entire dispensing of the product. When it is empty and the pressurizing gas has been dispelled, the can at that point is easily crushable by normal hand pressure."
In essence, the patent allows DCC to create a thinwalled D&I container and be patent-protected. Any and every competing can — regardless of how it's made, what material it's made of or how thin its walls are — that is easily crushable by hand-pressure when empty infringes on DCC's primary aerosol patent, claims Ross.
DCC cans meet the EU 18 bar specification and can be made to meet even the proposed future EU 22 bar specification.
Reduction of metal
Thinning the container walls allows DCC to reduce the metal content while gaining a cost advantage. In the UniCan D&I canmaking process, tinplate sheet is punched into round discs and formed into 1-3/4-in. high cups on a cupping press.
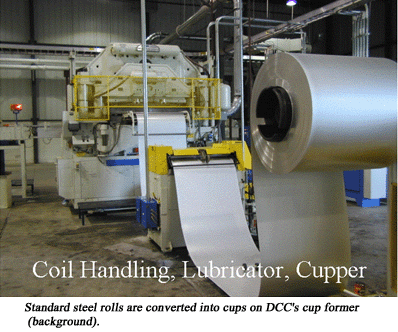
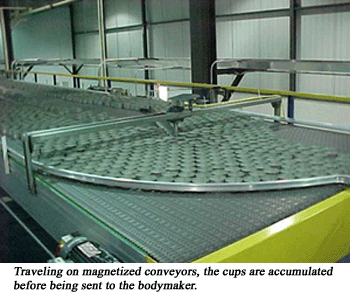
The tinplate cup starts out relatively thick to give the container bottom adequate support. The walls of the cup are then drawn into a full cylinder as the cup is punched through a series of rings. Each ring is slightly smaller in diameter than the preceding ring, resulting in a thinwalled cylinder approximately 0.0045-0.005-in. thick.
After the top edge of the cylinder is trimmed, the cans, which are conveyed on a magnetic conveyor, are sent through a patented screw-type washer and dryer. The container is optionally externally powder-coated and internally coated. The external heavy powder coating is sprayed onto the sides and bottom of the cans, adhering through an electrostatic charge. The interior can be supplied with a single or double coat "bake-on-bake" lacquer.
The durable monolithic external powder coat rustproofs the sides and bottom of the can, which is then necked and flanged to receive the aerosol dome (cone). The dome is seamed onto the can in a standard fashion. Finally, the cans are palletized and shrinkwrapped.
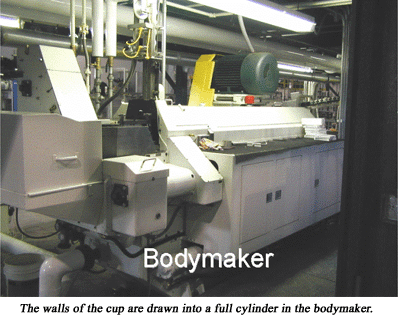
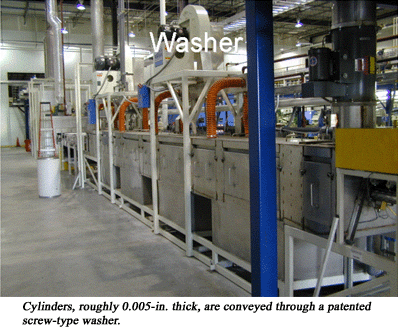
With the exception of the washer and external powder coater, the machinery is similar to that of a typical D&I soda can line. Decoration options will vary, but initially labels of various types will be the common choice.
Bend and crush
Perhaps the rarest benefit of the UniCan is that once its contents have been used up, the container can be bent and crushed, much like a beverage can. "You end up with a can that's easily and visually depressurized, safe, and can be easily recycled," says Ross. Conversely, after using a three-piece seamed aerosol can, which typically is about 0.008-in. thick, it will still be a pressurized, sealed vessel that must be punctured and degassed in order for it to be safely recycled.
"After the UniCan is crushed, it's like a steel food or beverage can and can go right through the recycling chain," says Ross.
In short, compared to conventional three-piece welded aerosol containers, the UniCan offers metal reduction of 25%-40%, greater ease of recycling since it's crushable, better aesthetics due to its seamless sides and bottom, and improved corrosion resistance and structural integrity because of its integral bottom and lack of a sideweld.
In 1998, DCC received a $425,000 grant from the U.S. Department of Energy for the metal reduction, energy savings, reduction of greenhouse gas emissions (indirect) and greater ease of recycling associated with its technology.
One line up, two to go
Dispensing Containers' first UniCan production line was installed at the Allentown plant in the first quarter of 2000, and commercial quantities of 202-diameter UniCans are currently available. The line, rated at a speed of 500 cans/min., is designed to produce 202-diameter cans in a minimum of four heights: 509, 605, 700 and 710. DCC expects that the line will produce 180-200 million cans annually.
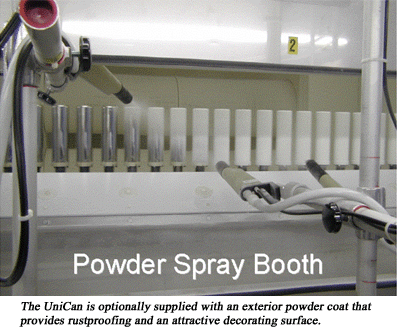
Ross says the company will install two more UniCan lines at the Allentown facility in the next 9-15 months: a 35mm line is scheduled for installation in the first half of 2001, and a 211-diameter line is planned for the fourth quarter of 2001. The 211 line will accommodate various can heights and will also be rated at 500 cans/min.
The UniCan, says Ross, is applicable to just about any aerosol application. Currently, DCC is offering solely aerosol spray cans, but the company is also planning to introduce a piston version of the can — UniCan B — suitable for viscous products like gels and caulks. The UniCan, says Ross, is well-suited for pistons because of its complete circularity — again, there's no sideweld that can potentially disrupt the circularity of the container body and, in turn, cause dispensing problems.
Next stage of evolution
The company is currently using conventional domes on the UniCan that it purchases from its licensee in Korea, Dae Ryuk Can Co. Ltd., one of two DCC licensees, the other being Cebal, a Pechiney S.A. subsidiary, which holds exclusive licenses for DCC technology in the European Union and also owns a 20% stake in the company. However, DCC also has patents on a lightweight dome that will save additional metal — up to 30% or 40% of the dome weight, says Ross. The lightweight dome is about 15-21 months away.
"When our lightweight can is used with our lightweight dome, the metal savings [over conventional welded aerosol cans] should be up to 40% for the complete package — can plus dome — depending on can size," Ross predicts.
"It's our belief that our can represents the next stage in the evolution of aerosol cans in the same way that David Reynolds' two-piece beverage can proved to be the next step in the evolution of the beverage can," says Ross, citing the can's metal savings, environmental benefits, attractiveness and corrosion resistance. "We believe it's the future of the industry."
DCC is currently looking for licensees or joint-venture partners outside of North America in countries that are not already covered by the Cebal or Dae Ryuk licenses. The company has no intention to license in the United States.
For more information: Dispensing Containers Corp., Tel: 610-336-9630, Fax: 610-336-9632, Email: l-ross@dispensingcontainers.com
Editor's Note: This article was first published in the September 2000 issue of CanTech International (www.cantechonline.com)