SUPER-WATER Jet Cutting of Packaging Foams
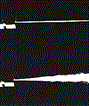
By W. Glenn Howells, Ph.D., Berkeley Chemical Research Inc.
SUPER-WATER [R] concentrated industrial water blasting additive was developed in 1974 and first used to clean hard intractable deposits from the Chevron, USA (Richmond, CA) ISOMAX hydroprocessing reactor exchangers in 24 hours. This is a task that, previously, using traditional methods, required three months. Later SUPER-WATER was used to remove carbonized epoxy-bound rubber from space-shuttle booster motors. This ultimately led to ultra-high pressure jet-cutting, at 48,000-50,000 psi, of an entire range of rubber materials and later to precision cutting of natural rubber-, polystyrene-, polyurethane-, EPDM rubber- and polyethylene-foams.
Companies providing contract-cutting evaluations of SUPER-WATER are listed together with safety and environmental considerations.
Table of Contents
Objective and Background
Cutting Materials With Super-Water
Cutting Packaging Foams With SUPER-WATER
Cutting Polyethylene Foam
Horsepower Reduction
Reduced Substrate Wetting
Cost-Effectiveness
Critical Importance of SUPER-WATER Injection Systems
Safety and Environmental Considerations
Objective And Background
There are many cost-effective advantages in using SUPER-WATER jetting at ultra-high pressure to cut specific packaging foams. These include more precise cutting at higher speeds accompanied by a 38% reduction in equipment operating and maintenance costs, a 31% reduction in horsepower requirement and an increase of up to six times in waterjet nozzle lifetime.
SUPER-WATER was first used in 1974 to clean Chevron USA ISOMAX hydroprocessing reactor exchangers in approximately 24 hours, a task that previously required three months1. The SUPER-WATER polymer, a linear macromolecular partially hydrolyzed polyacrylamide (with a molecular weight of 16 to 18 million), when dissolved in water at low concentrations (typically 0.1% to 0.3%), greatly increases cutting efficiency.
Three steps make SUPER-WATER more effective than plain waterjetting2:
Drag reduction (of at least 50%), resulting in nozzle pressures more closely matching pump pressures.
Jet focusing, which provides increased power density on the target.
Macromolecular bombardment. Because SUPER-WATER molecules have a molecular weight ranging from 16 to 18 million, or an average of 17 million, at supersonic velocities they behave as though they are rigid, greatly enhancing bombardment on a substrate.
"All molecules undergo varying degrees of intramolecular vibration. One may envisage intramolecular stretching, bending, and twisting and appreciate that the larger the molecule, the greater will be the time frames of these motions. During high-pressure polymerblasting with jets often impacting at supersonic speeds, the SUPER-WATER macromolecules and their associated aggregates of water do not have sufficient time for complete stretching, bending or twisting. As a result, the jet's effectiveness on the target is enhanced by bombardment with molecules that are "rigid." The Deborah number, D, is related to this effect. D is defined as the ratio between a polymer aggregate's relaxation time and the characteristic time scale during which the fluid stream undergoes deceleration. It is predicted that when D is greater than unity, "solid-like" behavior is exhibited because the polymer aggregate has an inadequate opportunity to adjust (relax) to its changing environment."2
SUPER-WATER functions by imparting more structure to water, and it does so by hydrogen-bonding large aggregates of water molecules. In the liquid phase, water molecules do not exist as individual entities. For example, two adjacent molecules of water are hydrogen-bonded to one another. The partial positive charge of a hydrogen atom on one molecule is electrostatically attracted to the partial negative charge on the oxygen atom of the other molecule.
Because the individual monomeric acrylamide and acrylic acid groups of SUPER-WATER are themselves each capable of hydrogen-bonding 13 to 14 water molecules, extended aggregates are formed. (Calculation, based on an average molecular weight of 17 million for the SUPER-WATER macromolecule and an average molecular weight of 80 for the monomeric units, shows that each molecule of SUPER-WATER bonds 2.9 million water molecules). The extended aggregates have been likened to a series of spinal columns, or polymer backbones within the bulk of a volume of water, as well as to the reinforcement bars used in concrete structures to develop overall strength.
Such longitudinal structures of cylindrically oriented water sheaths around the linear SUPER-WATER macromolecules would be expected to promote or stabilize laminar flow2 and decrease turbulence or the formation of vortices in boundary layers. This could be the basis for drag reduction, which, from a mathematical standpoint, is a poorly understood phenomenon. Furthermore the extended macrostructure is retained after emergence from the nozzle. This is manifested as a well focused jet as shown in Figure 1.
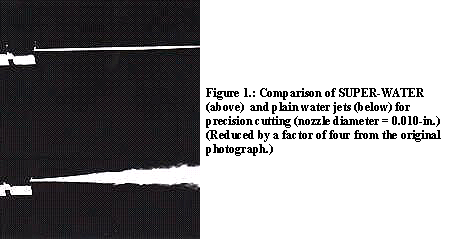
When SUPER-WATER jets are traveling at supersonic speeds, it is tempting to assume the SUPER-WATER molecules and their associated aggregates of water are linearly aligned in the direction of flow. It is not necessary to assume this, however, because on a molecular level, cordoned, helical or any ordered or extended macrostructure would bring about the observed jet focusing. The important point is structure is imparted to the water2.
Cutting Materials With Super-Water
The drag reduction of SUPER-WATER results in lubricity, and, consequently, ultra-high pressure intensifiers and nozzles experience less wear. For intensifiers, this translates to a 38% reduction in operating and maintenance costs3 and for diamond nozzles a lifetime extension of 2.8-6.0 times.
The edges of clay rubber shoe soles cut with plain water and SUPER-WATER at 0.32 gpm are shown in Figure 2. These photographs, obtained at a magnification of eight times, clearly show the difference in quality of cut.
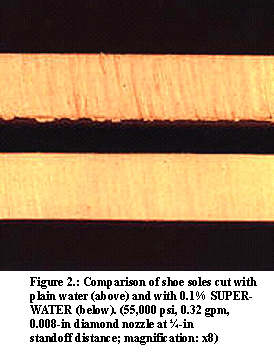
A 0.1% solution of SUPER-WATER costs approximately three cents/gallon after dilution of SUPER-WATER concentrate by a factor of 1,000. These advantages for cutting shoe soles, therefore, cost 57.6 cents/hour for the SUPER-WATER (or 0.32 x 3 cents x 60 = 57.6). SUPER-WATER cuts are smooth and have markedly less striations, and good surfaces are provided for subsequent adhesion processes. Additionally, this technique includes the absence of a heat affected zone (HAZ) and the related mechanical distortion that occurs using many mechanical cutting methods.
Cutting Packaging Foams With SUPER-WATER
In 1987, Yazici and Summers presented a description of cutting foam with SUPER-WATER in comparison to plain water4 using a series of factorial design experiments. For foam rubber, polystyrene foam and soft polyurethane foam, five parameters were varied including: traverse speed, pump pressure, diameter of the waterjet nozzle, concentration of SUPER-WATER and foam density. Equations were developed interrelating these five parameters.
One conclusion was that for foam rubber (density 66 Kg/cubic meter) the depth of cut increased with increasing SUPER-WATER concentration, and the quality of cut was much superior over the entire depth of up to 15-in. Both of these factors are important because the studies were targeted at determining the ideal way of cutting foam rubber used in U.S. Navy packaging stores to be shipped around the world; consequently tight tolerances were essential to ensure a close fit.
Summers showed the depth of cut is, in essence, linearly related to jet pressure, is in a power relationship with nozzle diameter and an inverse power relationship with traverse speed and increases with the concentration of SUPER-WATER:
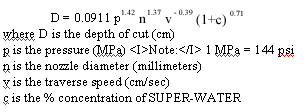
From the average specific energy data, the most efficient combination for cutting these 15-in foams involves high traverse speeds, large and intermediate nozzle diameters and pressures below 14,400 psi. The particular choice of these parameters varies with changes in the type of foam4.
The results obtained by Summers on foam rubber, polystyrene foam and soft polyurethane foam have now been extrapolated to other foam products such as polyethylene.
Cutting Polyethylene Foam
The following polyethylene substrates were cut (as reported by PCF Foam Corp. of Ohio (Cincinnati)):
Item A: 2-in thick 4# Crosslink (super-small pore size crosslinked polyethylene foam with a density 4-lb per cu ft) for reusable packaging.
Item B: 2-in thick 6# Crosslink (density 6-lb per cu ft) for automotive reusable packaging and reusable packing racks.
Item C: 3-in thick version of Item B.
Use of plain water on these materials indicated they could be cut with the required accuracy using a pump pressure of 46,000 psi, a flow rate of ¼ gpm and a sapphire nozzle (diameter of 0.008-in) at a 1/8-in standoff distance. However compared to plain water, 0.3% SUPER-WATER at 46,000 psi, ¼ gpm, a standoff distance of 1/8-in and only a 0.007-in nozzle used on 1,300 pieces of Item A, 2,700 pieces of Item B and 7,400 of Item C gave an equal edge quality and increased cut speeds by 250%, 300% and 290%, respectively. Strict dimensional and geometric requirements were obtained by computer aided design (CAD).
Figure 3a-c shows Items A, B and C in profile (or side elevation). It should be noted that these drawings are not to scale in either an absolute or relative sense.
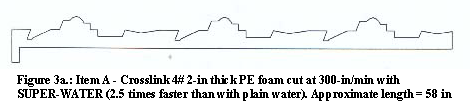

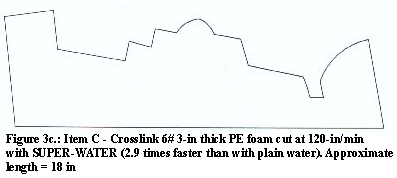
Figure 4 shows photographs of Items B and C (the length of Item A caused its photographs to be distorted).
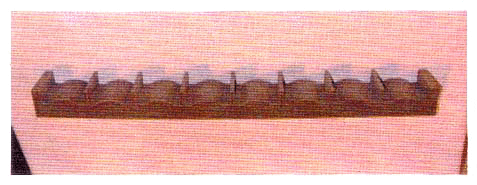
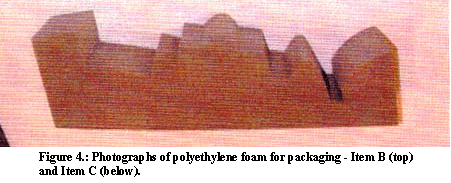
The overall project, carried out with an Ingersoll Rand 40 HP Streamline-I intensifier, was completed approximately three times faster than if plain water had been used.
Because of the success obtained in cutting the PCF Foam material, samples of Pactiv Corp.'s (Lake Forest, IL) (formerly Tenneco Packaging) PolyPlank closed-cell polyethylene foam were tested. PolyPlank, according to the company, is virtually impermeable to water, buoyant and highly resistant to water vapor transmission. It comes in a wide range of densities and a variety of colors with standard options including: pink, which is anti-statically treated for electronic applications; natural, which is fire-retardant; blue, made of reclaimed material; white; and black.
Waterjet Inc. (Columbus, IN) was provided with three of the Pactiv samples. Results with plain water were obtained at 50,000 psi, ¼ gpm, and at a standoff distance of 1/8-in using a 0.008-in nozzle. With just a 0.007-in. nozzle and 0.3% SUPER-WATER, edge qualities were achieved that equaled those obtained with plain water. However, with SUPER-WATER the cut speeds were significantly faster.
The three samples were cut as follows:
The first sample, 2½-in thick PP224108-4# polyethylene (with a density of 4-lb per cu ft), was cut with SUPER-WATER at 60-in per min. versus plain water at 40-in per min. a 50% increase in cutting speed.
The second sample, 3-in thick RLPP324108 (reclaimed material), was cut with SUPER-WATER at 300-in per min. versus plain water at 120-in per min. a 250% increase in cutting speed.
The third sample, 2¼-in thick FRPP224108 (flame retardant), was cut with SUPER-WATER at 180-in per min. versus plain water at 90-in per min. a 100% increase in cutting speed.
Based on these results, cutting PolyPlank closed-cell polyethylene foam with SUPER-WATER clearly has potential. As previously noted, a smaller nozzle (e.g., 0.007-in.) using SUPER-WATER requires less horsepower than the larger 0.008-in. used with plain water.
Horsepower Reduction
Results of cutting EPDM closed-celled rubber sponge are provided in Table 15. (Editor's note: The client requested anonymity.) The results for 0.3% SUPER-WATER with a 0.007-in sapphire orifice are provided in parenthesis, while the results using plain water with a 0.008-in. sapphire orifice are listed without parenthesis.
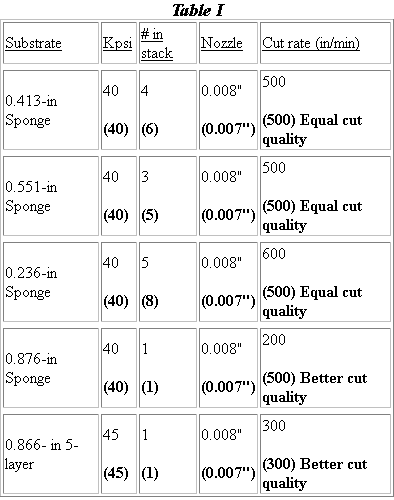
The client wished to reduce the required horsepower and increase the number of layers in the stack being cut. Using SUPER-WATER, either the number in the stack was increased (from 4 to 6, 3 to 5 and 5 to 8) with the same cut quality or, in two cases, the same number in the stack was cut but with improved cut quality. By using a 0.007-in nozzle with SUPER-WATER instead of a 0.008-in. nozzle with plain water, a decrease in required horsepower of 31% (i.e. from 10.1 to 7.0 horsepower) was achieved5.
In the packaging industry (as well as in print and die-cutting operations) Durometer 55-60 EPDM resins are extruded into different profiles for use as ejection material in flatbed dies and rotary steel dies. These Durometer 55-60 EPDM resins will likely be as amenable to cutting with SUPER-WATER as the EPDM materials tabulated in Table 1. This is because, previously, 90 Durometer rubber (4-ply and 1-in thick) was cut at 49 in/min. with a 0.3% SUPER-WATER solution (0.22 gpm at 48,500 psi) and a 0.007-in. nozzle at a standoff distance of 1/16-in and, notably, with a virtual absence of striations6. Under the same conditions, cuts with plain water were slower (39 in./min.) and had very marked striations6.
Reduced Substrate Wetting
SUPER-WATER reduces the wetting of substrates2, 6, as would be expected from a jet in air characterized by distinct coherence and an essential absence of spray, as shown in Figure 1. (The diameters and lengths of the jets and nozzle housing shown in Figure 1 are less than actual size. Thus the orifice container is 1.125-in in diameter, the inset diamond nozzle has an internal diameter of 0.01-in and the photographed length of both jets is actually 6.9-in).
Because of the absence of spray, the tendency for a SUPER-WATER jet to wet substrates is diminished. For example, with its incisive cutting ability, SUPER-WATER successfully removed 20,000-sqft of adhesive-attached cork from a concrete ceiling. By contrast, plain waterjet fluid, with its inevitable associated spray, was completely absorbed by the 8-in. thick layer of cork, which was virtually unaffected and remained in place2, 6.
Similarly the extent of a SUPER-WATER jet's coherence which can be correlated with the effectiveness of cutting thick materials may be seen in the following examples: Tree bark was removed at 10,000 psi and 10 gpm at a standoff distance of 40-ft with a 0.06-in nozzle2, 6. Also, a 1-in hole was drilled in 5/8-in thick plywood in 5-8 seconds at a standoff distance of 10-ft using 9,000 psi, 12 gpm and a 0.067-in nozzle. A plain waterjet merely wets the plywood2, 6.
Cost-Effectiveness
Over a three-year period, cost-effectiveness was determined using a Flow International intensifier at 40,000-45,000 psi7. The results parallel those for precision cutting of other materials6.
Relative to plain water, use of SUPER-WATER was found to improve the quality of cut, i.e. no subsequent sanding is required, saving $15,000 annually in labor costs7. It also increased cutting speed by 30%-200%, providing an estimated annual production increase of $420,000 in receivables7. Additionally, it was found to reduce intensifier operating and maintenance costs by 38%, i.e. from $11.12/hr in 1993 to $6.86/hr in 1996 is a reduction of $4.26/hr. The annual operating savings are $1,0257.
For an annual expenditure of $200 for SUPER-WATER, Decoustics (Toronto) reportedly achieves a return on investment (ROI) of >2,000 to 17. This application, which is for cutting fiberglass acoustic panels ranging from 3.2-millimeters (1/8-in) to 101.6-millimeters (4-in) thick, gives an unambiguous demonstration of the economic advantages of using SUPER-WATER in ultra-high pressure waterjet cutting.
Critical Importance of SUPER-WATER Injection Systems
SUPER-WATER, as sold, is in the form of a water-in-oil emulsion. The internal water phase contains the polyacrylamide. In order to use the product, the emulsion has to be broken or, to be exact, inverted to an oil-in-water emulsion. This absolutely necessitates use of specific types of injection systems which, placed after the filters, accurately meter the requisite amount of SUPER-WATER into the water stream.
Filters cause elongational shearing of macromolecules, leading to a reduction in molecular weight and a parallel reduction in effectiveness2. A brief description of "elongational shearing" is as follows:
In solution, the macromolecular molecules of SUPER-WATER and their associated aggregates of water are coiled, although they might adopt some measure of linearity under conditions of flow. In passage through filters (or during centrifugal pumping, which must also be avoided) the hydrogen-bonded aggregates of water would be "stripped away," exposing the carbon-carbon backbone. The backbone while being elongated would be readily accessible, and shearing by carbon-carbon bond scission will occur2. The diluted SUPER-WATER then flows through a static mixer, in which complete and uniform emulsion inversion is ensured, to the main stream of the waterjetting fluid.
Prior to use, SUPER-WATER requires five to six minutes at 70°F to become fully hydrated. As mentioned previously, the active ingredients in SUPER-WATER are macromolecular partially hydrolyzed polyacrylamides with a molecular weight ranging from 16 to 18 million, so the bonding of water molecules (or hydration) takes a finite time. This is because each monomeric unit of polyacrylic acid and of polyacrylamide bonds 13 to 14 molecules of water2. Obviously this bonding of polymer and water cannot take place instantaneously because it must proceed by formation of sequential layers of the 13 to 14 water molecules to finally furnish 2.9 million water molecules bonded to each SUPER-WATER macromolecule.
The hydration can be achieved in either a holding tank, a bank of polyvinyl chloride tubing (as shown in Figure 5) or in a length of low pressure tubing. The top left photograph in Figure 5 shows two light-blue filters (with white labels) located on the incoming municipal water stream before the entire intensifier system. The top right photograph shows a closeup of the non-electrical proportional DOSATRON injection unit (blue color with two white labels) with a plastic tube withdrawing from its bottom port (white liquid) SUPER-WATER from a half-gallon plastic container. Plain water enters the DOSATRON unit at the left port, and the exiting SUPER-WATER solution (at the right port of the DOSATRON unit) then flows downward through a (black) static mixer.
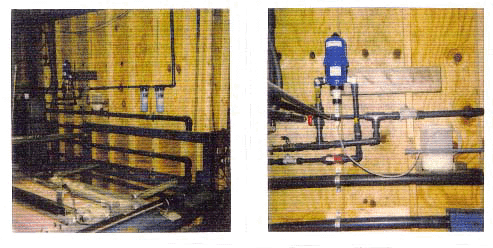
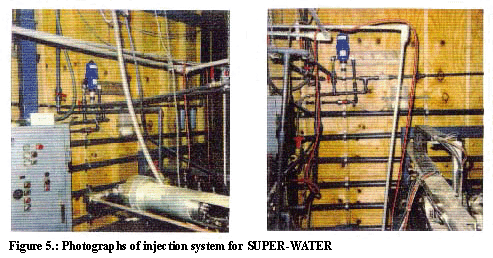
The bottom left photograph allows a partial view of the Ingersoll Rand intensifier and its control panel, while the bottom right photograph shows more clearly the system of the horizontally positioned bank of (dark green) tubes, in which hydration of the SUPER-WATER takes place.
The flow path is arranged so that the hydration of SUPER-WATER takes place from bottom to top prior to entering the intensifier. With this "bottom-to-top" flow pattern, if any partial separation of water and SUPER-WATER takes place on standing overnight, the system "self-flushes" itself and the fluid is readily returned to a homogeneous condition.
Appropriate lengths of tubing may be calculated by knowing the flow rate, and that complete hydration takes six minutes at 70°F, (or three minutes at 88°F, or 12 minutes at 52°F). For example at a flow rate of one gallon/minute at 70°F, one requires 40 feet of 2-in. polyvinyl chloride pipe (i.d. 1.95-inches).
The preferred injection systems are non-electrical proportional liquid dispensers available from DOSATRON International Inc. (Clearwater, FL, Tel: 800-523-8499, Email: mail@dosatronusa.com) or Weber Lubrifiants, Sa, (Rixheim, Cedex, France, Tel: 333-89 65 40 70, Email: info@weberlub.com.
Safety And Environmental Considerations
The usual safety precautions employed during hydroblasting8 are appropriate for ultra-high pressure precision cutting with SUPER-WATER. Because of its incisive cutting ability, SUPER-WATER must be handled with very great care. The OSHA Material Safety Data Sheet for SUPER-WATER describes general precautions, but it should be noted that upon appropriate dilution (i.e. 0.1%-0.3%), the properties, apart from flow characteristics, closely approach those of water.
Neither polyacrylamide nor polyacrylic acid, or combinations, are listed in the EPA Consent Decree9, nor are they included in the list of chemicals described as being carcinogenic10.
SUPER-WATER is biodegradable and does not foul oxidation ponds2. The chemical oxygen demand of SUPER-WATER is 706 g/L (at a use concentration of 0.1% it is 0.7 g/L), and the biological oxygen demand is 87 g/L (at 0.1% it is 0.09 g/L). The LC 50/96 hr is 53 ppm (Rainbow Trout) and 84 ppm (Blue Gill Sunfish). The acute oral toxicity (rat) is >10 ml/Kg and the dermal toxicity LC 50 (rabbit) is also >10 ml/Kg.
SUPER-WATER conforms to the Federal Food, Drug and Cosmetic Act as amended in 1958 and 1960, specifically Chapter 21 CFR, Section 176.110 as a component of paper and paperboard in contact with food and Section 175.105 as a component of adhesives in contact with food. Other SUPER-WATER components conform to CFR 21, Sections 178.3400 and 178.3650.
Because SUPER-WATER is a "non-regulated material, liquid, cleaning compound, NMFC 48580 class 55," it is shipped by truck, ship, and air, including UPS.
Acknowledgements: The author appreciates and acknowledges the contributions of Vincent L. Imlay of Waterjet Inc. (Columbus, IN), Renato Lombari of Soheil Mosun Ltd. (Toronto), Jeff Huhn of PCF Foam of Ohio (Cincinnati) and Steven Nau of Pactiv Corp. (Forest Hills, IL) who provided samples for the studies for this paper.
References
1. D. Alexander and J. T. Regan, "Polymer blasting eliminates hard deposits in refinery heat exchangers," Chemical Processing, May 1984.
2. W. G. Howells, "Polymerblasting with SUPER-WATER [R] from 1974-1989: a Review," International Journal of Water Jet Technology, Volume 1, Number 1, (March 1990), pp. 1-16.
3. R. Lombari, letter to the Editor, ..."the longevity of our consumable jet components due to the lubricity of SUPER-WATER," Jet News, Water Jet Technology Association, St. Louis, November 1996, pp. 2 and 11.
4. S. Yazici and D. A. Summers, "The Use of High Pressure Waterjets in Cutting Foam," Proceedings of the 4th American Waterjet Conference, Berkeley, California, (August 26-28, 1987), pp. 11-18.
See also "Waterjetting Technology" by David A. Summers, published by E & FN Spon, an imprint of Chapman & Hall, 2-6 Boundary Row, London SE1 8HN, U.K., (ISBN 0 419 19660 9).
5. Advertisement by Berkeley Chemical Research Inc., in Jet News, October 1999, reporting data obtained by Vincent M. Imlay, Waterjet Inc., Columbus, Indiana.
6. W. G. Howells, "SUPER-WATER [R] jetting applications from 1974 to 1999," Proceedings of the 10th American Wateriet Conference, Houston, (August 14-17, 1999), pp. 363-380.
7. R. Lombari, "Ultra-High Pressure Non-Abrasive Polymer Jetting: a Production Implementation," Proceedings of the 9th American Waterjet Conference, Dearborn, Michigan, (August 23-26, 1997), Paper 17, pp. 251-266.
8. "Recommended Practices for the Use of Manually Operated High-Pressure Water Jet Equipment," issued by the Water Jet Technology Association, St. Louis.
9. Q. B. Stork et al., Journal of Chromatographic Science, Vol. 18, November 1980.
10. Second Annual Report on Carcinogens, December 1981, U.S. Department of Health & Human Services, Public Health Services (National Toxicology Program).
About the Author: W. Glenn Howells formed Berkeley Chemical Research Inc. (Berkeley, CA) in 1974 and was a founding member of the Waterjet Technology Association in 1983. He received a B.Sc. in chemistry from the University of Southampton (U.K.) in 1955, was employed by Shell Refining and Marketing Co. in the U.K. and then received a Ph.D. in organic chemistry from Brandeis University in 1961. After conducting postdoctoral research for two years, he worked for four years at Chevron Research Co. (Richmond, CA) and for three years at MacMillan Bloedel Research, Ltd. (Vancouver, B.C., Canada). Howells joined the University of California, Berkeley as an Associate Research Chemist in 1970.
For more information:
Berkeley Chemical Research Inc., W. Glenn Howells, Tel: 510-526-6272, Fax: 510-525-2375, Email: WGlennHowells@webtv.net, Website: www.berkeleychemical.com.
Waterjet Inc., Vince L. Imlay, Tel: 812-523-2040, Fax: 812-524-1291, Email: hijet@hsonline.net
Soheil Mosun Ltd., Waterjetting Division, Renato Lombari, Tel: 888-446-6786, Fax: 416-243-7132, Website: www.soheilmosun.com.