EMERGING TECHNOLOGIES: Is eliminating PVC from IV bags the real issue?
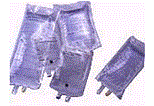
By Steve Mogensen
Allied Development Corp.
There has long been overriding pressure from environmental and healthcare groups to see polyvinyl chloride (PVC) eliminated from IV bags. For packaging suppliers, however, purging PVC from IV bags is not the real issue, and here's why.
PVC is the main polymer used to fabricate films for flexible parenteral packages, i.e. IV bags. PVC is also a source of major controversy for this industry. There are two claims being levied against PVC that have very serious health implications if they are true:
- Plasticizers are included in PVC resin formulations used for film in order to soften the PVC and make it flexible enough to be made into a pliable film. Critics believe the PVC plasticizer leaches out of the bag into the IV solution. Some of these plasticizers are suspected carcinogens.
- PVC may also have an impact on the environment when it is incinerated. It is believed to release toxins into the air as byproducts of the incineration process.
The true impact of the claims against PVC is hard to determine, because there is strong evidence and expert opinion on both sides of the issue. Regardless of whether the claims are true, there is heavy pressure on the IV solution providers to change IV bags to something other than PVC. This creates a market opportunity for any company that can provide a solution.
Tough market to penetrate
However, for packaging suppliers the situation is not so simple. To begin with, IV bags are one of the few flexible packaging formats manufactured from resin by the end-use provider. For example, companies like Baxter International, the inventor of the PVC IV bag, manufacture both the IV solutions and the bag. Baxter and most other major industry participants maintain packaging research and PVC film manufacturing as internal activities. Even more to the point, B. Braun is marketing a non-PVC packaging solution independent of their IV solutions.
Today's business models teach focus on core competencies, and the extent of the focus on packaging in this industry could be considered outside the core competencies of end-users — and perhaps best left to packaging producers. There are some indications that these companies are beginning to move towards such logic however slight the move may be. The end result is a very difficult market for packaging producers to penetrate.
In addition to the challenges created by the vertical integration of the current market participants, packaging for IV solutions must meet difficult technical requirements. The IV bag must have:
Highly concentrated industry
Another challenge, and perhaps the most important one, is the fact that the PVC bag is very low cost. One factor affecting the economics is the highly concentrated nature of the business in Europe and North America. Three suppliers hold 80%-85% of the market in both regions:
The concentrated nature of the industry has created a lot of competition, and the cost structure has been pushed downward. PVC is an inexpensive resin, and the vertical integration of the IV bag manufacturing process has already squeezed out a lot of cost from the production process.
Non-PVC solutions
Eastman Chemical Co. is devoting significant resources to the medical market, and according to Marie Wilson, business market manager, "non-PVC solutions do exist from B. Braun and packaging suppliers like Cryovac and the Sengawald business of Pactiv. Both B.Braun and Cryovac use our Ecdel elastomer products in their formulations."
In fact these bags may offer some technical advantages. According to Jake Chadwick, general manager, Medical Packaging Business for Cryovac Sealed Air, "our product offers performance beyond PVC bags in the following ways":
Still, the bottom line remains that the commercial success of non-PVC bags to date has been limited to the use of these bags in niche situations. On a global basis, non-PVC bags command approximately 5% of the market (See Figure 1).
Figure 1: Packaging Formats for IV Solutions - Global Basis
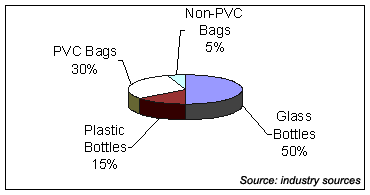
Opportunity knocks for packaging companies
So why and how are the companies that produce packaging as a core competency trying to penetrate this market?
The reason is because the packaging market for IV solutions is a substantial one. On a global basis, industry participants estimate there are 4 billion containers consumed each year. A number of packaging formats are used, and the distribution is shown in Figure 1.
Another reason to pursue this market is clearly evident from Figure 1 — half of the market is in glass bottles (virtually all of the glass bottle consumption is in Asia and Latin America). Surely, there is little optimism that a significant shift will occur to non-PVC bags from PVC bags or plastic bottles anytime soon because of the long list of business and technical issues discussed earlier. However, it is quite certain that the glass bottle format will ultimately shift to other formats as has been done in North America and Europe.
Market strategies
So how are flexible packaging companies (non IV solution producers) approaching the market?
One way is to provide good products and good technical solutions. Current products may not be as economical as PVC but can provide good value in certain situations.
Another possibility is to work on the opportunity in Asia. Solution providers in bottles are or will be faced with a decision about what packaging format to use for their next-generation package. A move to PVC products must be carefully considered because of the overhanging health and environment issues. According to Chadwick, "We are achieving satisfactory results with our non-PVC IV products, with a significant contribution coming from China, Korea and other Asian countries. Many companies in Asia are leapfrogging the PVC situation and going directly to non-PVC solutions."
In Europe and North America there is a need to establish a presence and familiarity with the solution providers. An established relationship will probably be necessary for any packaging company to become a significant supplier to this industry.
Speeding the pace of change
Packaging materials are part of the drug approval system for IV solutions, so new packaging materials must be tested and submitted to the FDA. The installed capital equipment base at fully integrated solution providers is very large. These and other issues mentioned earlier create an environment of slow change in this industry.
However, a sophisticated non-PVC film product with sophisticated processing requirements (in a business environment emphasizing focus on core competency) may ultimately win a significant share of the worldwide business for the packaging industry. A catalyst such as a significant clarification of a PVC health risk might speed things up in Europe and North America.
For more information:
Eastman Chemical, Suzanne Manis, Tel: 423-229-1424
Cryovac Sealed Air, Tel: 800-845-3456