Electron-Beam Irradiation of Packaged Foods
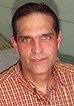
By Judy Rice, Contributing Writer
Table of Contents
Need for Packaging Options
Food Safety is Driver
Tyson/Titan Alliance
Electron-beam irradiation technology has promising potential for on-line sterilization of many packaged foods. By directing accelerated electrons at the passing packages, processors can kill pathogenic bacteria on product and package surfaces as well as up to about three inches below product surfaces. E-B does not provide the deep penetration offered by gamma irradiation. But E-B is quicker and does not carry the radioactive waste residue concerns sometimes associated with gamma systems, which use Cobalt or Cesium as a power source.
In fairness to gamma technologies, it should be noted that efforts are made to recycle any such residues. And nearly a dozen packaging materials with commercial relevance are routinely gamma irradiated today, including polyethylene, polyvinyl chloride (PVC), polyvinyldene chloride (PVDC), nylon 6 and ethyl vinyl acetate (EVA). Gamma irradiation often is used to treat bulk-packed products such as spices. Still, the "NIMBY" (not in my backyard) syndrome has been a concern with gamma irradiation.
Need for Packaging Options
In contrast to gamma irradiation, broad commercialization of E-B has been obstructed by two things: cost and lack of packaging material options. As Dr. George Sadler, research professor of food packaging at the Illinois Institute of Technology's National Center for Food Safety & Technology, notes, "E-B systems have been around since the 1950s, but until fairly recently the cost of operation was high. Only one company, Cryovac, sought and obtained clearance from the Food and Drug Administration for the use of a packaging material for E-B-treated packaged products — EVA."

Sadler continued: "Most other films were approved in the 1960s for gamma irradiation only. These approvals were sought for military and NASA feeding programs. Over time, E-B costs have eased down, and interest in the technology has increased in the food and packaging industries." Sadler says that now the challenge is to expand the list of packaging material options allowable for E-B processing.
Dr. Sadler heads up a task force of about 20 companies (primarily resin suppliers and packaging converters such as Dow, DuPont, Cryovac and American National Can) working to gain FDA clearances for additional packaging films, as well as for some semi-rigid and rigid plastic-based structures.
"Using a linear electron-beam accelerator at the SteriGenics facility in Schaumburg, IL, we're testing and developing documentation for such materials as ethyl vinyl alcohol (EVOH), certain nylons, all ionomers and anhydrite grafted polyethylene. We started the task force about a year-and-a-half ago and hope to submit petitions to FDA for at least six materials before Christmas," Sadler reports.
Food Safety is Driver
Asked about possible interactions between food products and packaging materials during the irradiation process, Sadler said, "We have done preliminary tests, and we don't get any compounds we didn't predict. And the ones we get are not there in high levels. We don't believe there is much opportunity for product/package interaction (packaging materials migration) except in minute amounts, and these would not compromise the food product."
Sadler added, "The interest in E-B treatment of packaged foods is food safety-driven. We expect fresh and processed meats will be among the first products to be marketed in E-B-treated packaging. There are some issues that need to be resolved, especially in terms of composite, multi-layer packaging materials and how they are affected by irradiation. But we are optimistic about E-B."
Sadler and the NCFST think this technology is the next natural step in the evolution of irradiation technologies for packaged foods. "First," he says, "there was gamma, now E-B, and the next step may include X-ray technologies. X-ray provides the quickness of E-B and the deep penetration of gamma. But right now, X-ray costs about 10 times more than E-B."
Tyson/Titan Alliance
In a related development, Tyson Foods Inc. (Springdale, AK) has announced plans to conduct some product development and test work with San Diego, CA-based Titan Corp.'s SureBeam(R) electronic pasteurization technology. Tyson joins some major beef processors such as IBP, Cargill and Emmpak in these test and development efforts. All these processors will have the benefit of a new Titan facility in Sioux City, Iowa.
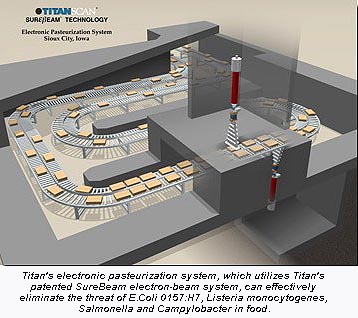
Tyson's chief marketing officer John Lea commented, "Through our alliance with Titan, we will be able to offer Tyson customers a greater choice of products. We chose the Titan system because it uses commercial electricity, not Cobalt 60, a radioactive material, to power either the X-ray or electron beam systems."
Both the FDA and the U.S. Department of Agriculture's Food Safety and Inspection Service have approved Titan's technology for use on meat and poultry. In a general position statement, Tyson states, "Tyson Foods Inc. believes that cold pasteurization (irradiation) has been scientifically proven to be a safe process which dramatically reduces harmful bacteria in food products, including poultry. Cold pasteurization can add valuable days of shelf life of refrigerated products, which improves the quality and safety of products delivered through existing distribution channels."
"We caution, however, that cold pasteurization is not a single-source solution to safe food. We recognize that, while reducing harmful bacteria, cold pasteurization also greatly reduces the number of competing (good) bacteria. Therefore, we strongly advocate continued adherence to the HACCP (Hazard Analysis and Critical Control Points) principles, GMPs (good manufacturing practices), standard sanitation operating procedures and other preventive programs for use in conjunction with cold pasteurization."
For more information:
For more information about the electron-beam irradiated packaging materials task force, contact Dr. George Sadler at the Illinois Institute of Technology's National Center for Food Safety & Technology, Tel: 708-563-1576. FDA guidance also is available at the Center.
For more information about SteriGenics food irradiation systems and services, contact Pat Adams, president of advanced applications, SteriGenics International Inc., Tel: 901-681-9006, or check the website at www.sterigenics.com.
For more information about Titan Corp.'s SureBeam electronic pasteurization technologies and the new Sioux City facility, contact the Titan Scan division at Tel: 858-552-9480, or check the website, www.titan.com.
About the Author: Judy Rice has been writing about the food and beverage industries for more than 20 years. She worked as the packaging editor for Food Processing magazine for more than 15 years. Prior to that, she worked at USDA's Food & Nutrition Service for seven years. She currently freelances for a range of trade publications and is a regular contributor to Packaging Network and other VerticalNet Inc. websites. She is based in Lac du Flambeau, WI.