Contract Packager Makes Chemical Packing Safer With Water-Soluble Films
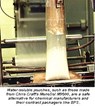
Table of Contents
Meeting Dual Challenges
Repackaging into Unit Doses
Safer-to-Handle Package
Customer Satisfaction
Although consumer environmental concerns regarding packaging are not commanding the attention they did, say, five years ago, such concerns are still a factor, particularly in the specialty chemical industry. Thus, companies continue to partner with packaging suppliers to address issues such as package waste disposal and end-user safety.
Water-soluble film packaging has emerged as a means for chemical producers to provide a cost-effective and responsible packaging alternative. Take Buckman Laboratories of Memphis, TN, for example, a manufacturer of specialty chemicals used in a variety of industries. The company went so far as to reformulate one of its products to take advantage of the safer handling benefits of packaging in water-soluble film pouches.
"Our chemical products are used to control scale, corrosion and microbiological problems associated with industrial water treatment processes," explains Rick Clark, water treatment product development manager at Buckman. "To control problematic microorganisms, we have to use some powerful chemical compounds that are difficult to handle. Our product labels warn of exposure hazards, but occasional contact still occurs. Accordingly, we are always looking for product application systems that are safer and more convenient for our customers."
Enter Bartlo Packaging Services (BPS), a West Helena, AR, contract packager that packages Buckman chemicals in pouches made of water-soluble film. BPS, which offers contract packaging services for the pesticide, herbicide and detergent industries, depends on Chris Craft Industrial Products (Gary, IN) to provide the water-soluble film that is compatible with these chemical products.
Meeting Dual Challenges
Water-soluble film addresses the dual challenges of container management and environmental safety, particularly for chemical and hazardous materials. Pre-measured unit doses, packaged in water-soluble pouches, provide a significant advantage over traditional bulk packaging methods. These pouches are contained inside secondary packaging, preventing direct contact between the end-user and the chemical product as well as exposure to toxic, irritant and nuisance materials. Water-soluble unit-dose packaging, such as Chris Craft's latest advance, MonoSol 9500, minimizes risks for handlers, reduces pollution and eliminates product loss from spillage.
Chris Craft's M9500 is well suited for chemical manufacturers the film provides fast solubility at the point of use and offers improved resistance to embrittlement as well as excellent cold-storage capabilities. Appropriate for packaging neutral, mildly alkaline and acidic formulations, M9500 can be used for powder, gel and liquid forms of chemicals and detergents.
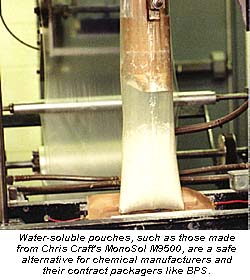
Agricultural chemical and other chemical product manufacturers use pouches made from water-soluble films to assure mixing accuracy. At the BPS West Helena facility, a variety of highly concentrated chemical products go into unit pouches between 1 gram to 100 pounds, some for multiple packs and some for single doses. A user-friendly secondary package may contain one or several MonoSol film-packaged unit doses of chemicals, depending on the application.
"Packaging in unit doses is where the agrochemical and cleaning products industry is headed," asserts Al Bartlo, president of BPS. "Chris Craft's water-soluble film enables unit dosage to be user-friendly."
Repackaging into Unit Doses
BPS uses 13 packaging lines to package a variety of chemicals ranging from high-activity detergents to highly toxic insecticides. Material arrives in drums or bulk delivery systems for BPS to repackage it into unit doses for industrial and commercial consumer use. BPS currently handles liquid, granular, powdered and gel chemicals.
When the bulk product is ready for packaging, it is transferred to hoppers on a floor above the packaging room. A level sensor in the hopper maintains the appropriate level of powder. The chemical is then conveyed from the hopper to a Chris Craft water-soluble film unit-dose pouch formed on a vertical form/fill/seal machine from Prodo-Pak Corp. (Garfield, NJ). For some applications, the film can either be preprinted or printed in-line to bear an identification, product name or part number.
The unit-dose pouches are then placed by hand into a secondary package. This package varies depending on the application. The outer package is sealed via a Chaffee (Burlingame, CA) rotor sealer, and lot numbers and other vital information are imprinted on the package with a Videojet (Wood Dale, IL) Excel printer.
BPS uses Chris Craft's state-of-the-art Product Compatibility Testing (PCT) Laboratory in Gary, IN, to specify correct films for its customers. Laboratory technicians perform the quantitative Fourier Transform Infrared Spectrophotometry (FTIR) analysis, which allows examination of the water-soluble film before and after exposure to the product. This test indicates if a particular film's composition changes after exposure to the customer's chemical compound an essential tool in predicting the long-term film/product performance.
Safer-to-Handle Package
As for Buckman, the company reformulated one of its products to utilize the inherent benefits of MonoSol water-soluble film such as safer handling. "In solid form, the water treatment chemicals can be easily mixed and packaged in a much safer-to-handle package," says Clark. "The total concept formulation and packaging is to limit human contact with the chemical and also to eliminate the need to dispose of waste packaging."
On the BPS automated packing line, the Buckman product is charged into water-soluble film, and then followed by placement in a waterproof, UV-resistant ziplock overpack to ensure product integrity.
Customer Satisfaction
Careful attention to both worker and product safety has resulted in tremendous growth for BPS, and the company continues its emphasis on safety and customer satisfaction. Part of its quality initiative leads BPS to continue working with suppliers known for quality.
"We are very satisfied with Chris Craft's level of technology," says Bartlo. "We've been using Chris Craft film since day one, and we've never had a single problem with it."
And for that, Buckman Laboratories, which constantly stresses safety and convenience for its customers, is grateful.
For more information:
Chris Craft Industrial Products Inc., 407 County Line Rd., Gary, IN 46403, Tel: 219-762-3165, Fax: 219-763-4477.
Prodo-Pak Corp., 77 Commerce St., P.O. Box 363, Garfield, NJ 07026, Tel: 973-772-4500, Fax: 973-772-0471.
Ralph Chaffee Co., 850 Mahler Rd., Burlingame, CA 94010, Tel: 650-259-1888, Fax: 650-692-7968.
Videojet Systems International Inc., 1500 Mittel Blvd., Wood Dale, IL 60191-1073, Tel: 630-860-7300, Fax: 630-616-3623.
Edited by Bill Noone