EMERGING TECHNOLOGIES: Will cyclic olefin copolymers be an effective packaging material?
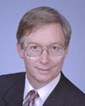
By Steve Mogensen, Allied Development Corp.
Cyclic Olefin Copolymers (COCs), a new family of resins, provide an interesting and unusual combination of properties for packaging films, with the potential to be an exciting new tool for packaging designers.
Some of the most important properties of COCs are excellent clarity, high stiffness, and very high barrier to moisture vapor. Because of these properties, COCs appear well-suited for flexible packaging applications such as blister packages, where they have the important advantage of being more environmentally friendly than some of the existing products.
Betting on pharmaceutical market
One company has made a significant new bet on COCs. Ticona, a business unit of Celanese AG, formally opened its Cyclic Olefin Copolymer (COC) resin production facility on September 26th, in Oberhausen, Germany. The facility has a nameplate capacity of 30,000 metric tons, which, according to industry sources, exceeds the capacity of all other producers combined.
The pharmaceutical market appears to hold great promise for these new materials. According to Geraldine Goverd, senior development specialist for Rexam Medical Packaging, "We intend to add two new products that utilize COCs to our commercial line by the end of the year. While we are still developing these products, they are now well-defined and will become part of our INTEGRApharm line of pharmaceutical packaging materials."
Rexam's existing INTEGRApharm product line includes PVDC-coated PVC films, which are the current standard of the blister pack industry. The new COC films will enhance the current product line by offering an alternative to standard materials. For example, Rexam's planned new 250 micron film made of polypropylene/tie/COC/tie/polypropylene will be comparable with 250 micron PVC coated with 40 or 60 gm/square meter of PVDC, with a target moisture barrier of 0.6g/m²-d.
The second film is expected to be a 330 micron film, similar in formulation to the first, that will compete with 90 gm/m² PVDC coated PVC, with a target moisture barrier of 0.23g/m²-d. Goverd says, "The 330 micron film will also be competitive with Aclar 22A film and better than SupRx 900, a much used Aclar lamination."
Competitive in many properties
Being competitive requires competitiveness with many properties, but the high moisture barrier, excellent clarity, PVC-like thermoformability, PVC-like toughness, ease of extruding and environmental friendliness of COC resins all appear very promising. According to Donal McNally, product manager for Ticona's Topas line of COCs, "Ticona's product is a copolymer of ethylene and norbornene. We have already begun our first commercial application of this copolymer in Indonesia."
McNally says that a multilayer film comprised of approximately 80% COC in the core layer protects Bayer aspirin in a blister pack. "Indonesia's climate, regionally hot and humid, put an extreme demand on the packaging requirements for moisture barrier. We are pleased that the COC-based film was chosen, and it shows the viability of COC in this application," says McNally.
Economics always play a key role in the success of new products, and this may limit the demand for COCs in the marketplace. With a list price of approximately $ 2.60 per pound, COCs must offer substantial value to justify such a price.
However, McNally says that high-volume pricing will be lower, due to increased manufacturing efficiencies. Comparing COC films to PVDC-coated PVC, the COC films require fewer manufacturing steps. According to Goverd, "The product cost may favor COCs because of the reduced cost of manufacturing, even with the high materials cost."
When a blister pack is formed the thermoformable film must be sealed to aluminum foil. Most existing foils for blister packs use a vinyl-based lacquer system to create the seal to PVDC-coated PVC films. COC films are anticipated to have polypropylene outer layers, which will not seal to a vinyl-based lacquer. The change to a new lacquer could increase system costs and hurt the viability of COC films for this application.
A matter of economics
The economics of COCs has undoubtedly been partly responsible for the fact that very little commercial success has been achieved with COCs. COCs have been available in the past from, for example, Mitsui and Nippon Zeon in Japan. Mitsui, at one time an R&D partner with Ticona, manufactures a copolymer of the same general type as Ticona, but with a different comonomer and catalyst. In fact, Rexam's source of materials for their testing up to now has been products manufactured by Mitsui, but purchased through Ticona. Rexam will be qualifying the resins from the Ticona manufacturing facility before introducing their products to the marketplace.
"COC resins have not been successful commercially up to the present time because the previous scale of manufacturing made them too expensive for broad use," says McNally. "The scale of Ticona's plant, coupled with the increased yield and efficiency obtained via our proprietary catalyst technology, has significantly reduced the cost of making these materials."
Other applications needed
Even if COCs are successful in pharmaceutical packaging, other applications are needed to make COCs a broad success. "We believe the properties of COC resins make it possible to use them as modifiers in blends or multilayer films," says McNally. "Their compatibility with LDPE and LLDPE create the possibility for blends that have improved film stiffness without diminishing other properties such as oxygen permeation and haze level. They can also be extruded as a discrete layer in a coextruded cast or blown film structure using existing equipment."
COCs have good chemical resistance to aqueous and oxygenated organic chemicals including hydrochloric and sulfuric acids, caustic soda, methanol and ethanol, but they are not suitable for use with high concentrations of fats, oils or aliphatic solvents such as hexane and toluene. Ticona COC resins have FDA Drug Master File and Device Master File numbers. Several grades meet U.S.P. Class 6 requirements and are also in compliance with FDA food contact requirements under conditions of use C through H.
The COC resins appear to improve hot-tack strength when added to polyethylene films as a modifier, and they add stiffness to polyethylene when added as a modifier. In addition, they create the potential to downgauge.
Possibilities in blisters Despite the long list of excellent properties, COC resins are still a relatively high-cost material for packaging applications. The cost will limit the applications that can utilize this new material. These properties appear to be very well matched to blister packaging requirements, and there is optimism that COCs may have commercial value in this marketplace.
Other clear-cut packaging markets where COCs can be competitive are not as easy to uncover. Still, COCs are an excellent addition to the group of resins that are one of the key building blocks of the packaging business.
For more information contact:
Ticona, Donal McNally Tel: 908-522-7544
Rexam Medical Packaging, Geraldine Goverd (44) 11-7987-2000
About the Author: Steve Mogensen is vice president of sales and marketing for Allied Development Corp., a Lakeville, MN, company that provides a variety of services to the packaging industry aimed at helping companies improve their revenue. Mr. Mogensen joined the startup company in 1996 after more than 20 years experience as a business and technology executive for Viskase Corp., Rexam PLC and the Graphic Packaging Division of ACX Technologies Inc. A Registered Professional Engineer, Mr. Mogensen has a B.S. in Engineering from the University of Illinois and an MBA from the University of Chicago/Lewis University.
Mr. Mogensen can be reached at: Allied Development Corp., 17689 Lake Oak Circle, Lakeville, MN 55044, Tel: 952-898-1832, Fax: 952-898-2242, Email: sam@allied-dev.com, Website: www.allied-dev.com.
Editor's Note: PackagingNetwork.com welcomes Steve Mogensen as a regular contributor. His "Emerging Technologies" articles offer insight into technology trends occurring in the packaging industry. Look for his column each month.